History / Growth
Innovation based on tradition
Everything started in 1968 with Peter Konrad Däbritz having his invention patented that became the namesake for Varioplast. Meanwhile, since 1970, with our location being in Germany, we have established our position as a leading company in the field of plastics injection moulding.
Having a steadily growing portfolio of innovations and being in an active exchange with our customers enables us to predict what is essential for the manufacture of new products and to offer extensive and efficient solutions.
Along the entire value chain from mould-making through injection moulding, joining technology and surface finishing techniques up to our own reusable packaging - VARIOBOXX® - we have established manifold process expertise and broad manufacturing techniques which are fully automated and interlinked.
Our inhouse automation team permanently develops new inline processes with the primary goal of applying these also for smaller production batches in an efficient and flexible way.
This is exemplified in our fully automated coating processes (expandable with multilayered coating, lasering technology...) and our fully automated PVD-metallization processes (expandable with lasering technology, ultrasonic welding technology...).
Our numerous customers in the industries of automotive and aviation, household appliances, electrical engineering and equipment technology, medical and building technology appreciate the benefits in terms of quality and competitive edge.
The high robot quota allows for highest reproducibility and efficiency and contributes significantly to the improvement of the ecological balance.
We adhere to a tradition of innovation and sustainability that reflects in eco-friendly production alternatives such as PVD-metallization and inline robot coating which enable us to reduce our ecological footprint by up to 75%. Our lightweight reusable packaging system VARIOBOXX®, made from recycled material (saving -5kg Co2/lorry/100 km compared to standard packaging), also contributes to this as well as our resource-conserving building equipment does.
Through our inhouse tool manufacture we can offer quick response times and flexibility. Our longterm European partners and a subsidiary in China enable us to secure the procurement of simple as well as complex moulds.
For these reasons we are not only best in class concerning product quality but we also have the competitive edge internationally.
Each service provided by Varioplast incorporates the entire expertise and in-depth understanding of the company for the needs and requirements of our customers.
Over 50 years of innovation history
1968
VARIOPOT® flexible growing system for plants
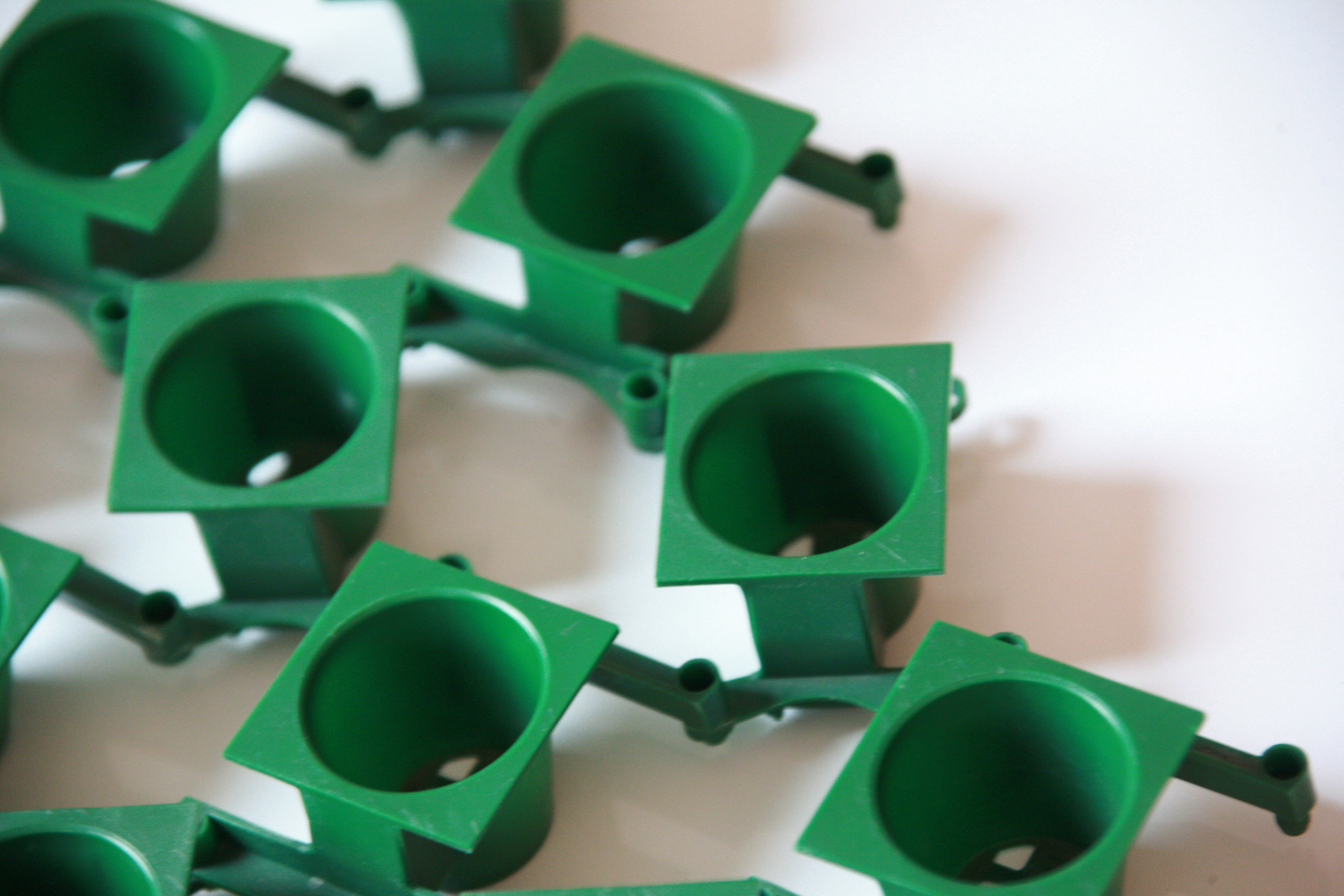
1970
The VARIOPOT® is the origin and trigger for the foundation of VARIOPLAST® Konrad Däbritz GmbH in 1970 in Horrheim near Stuttgart
1978
Relocation of the company to Ötisheim.
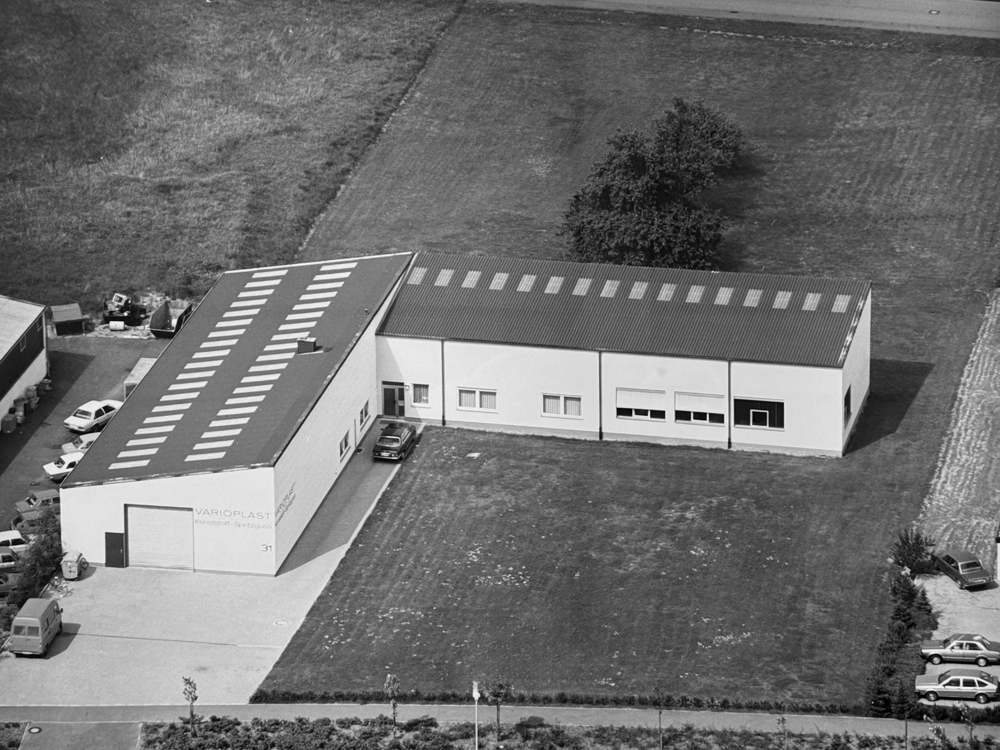
1984
Assembly hall extension
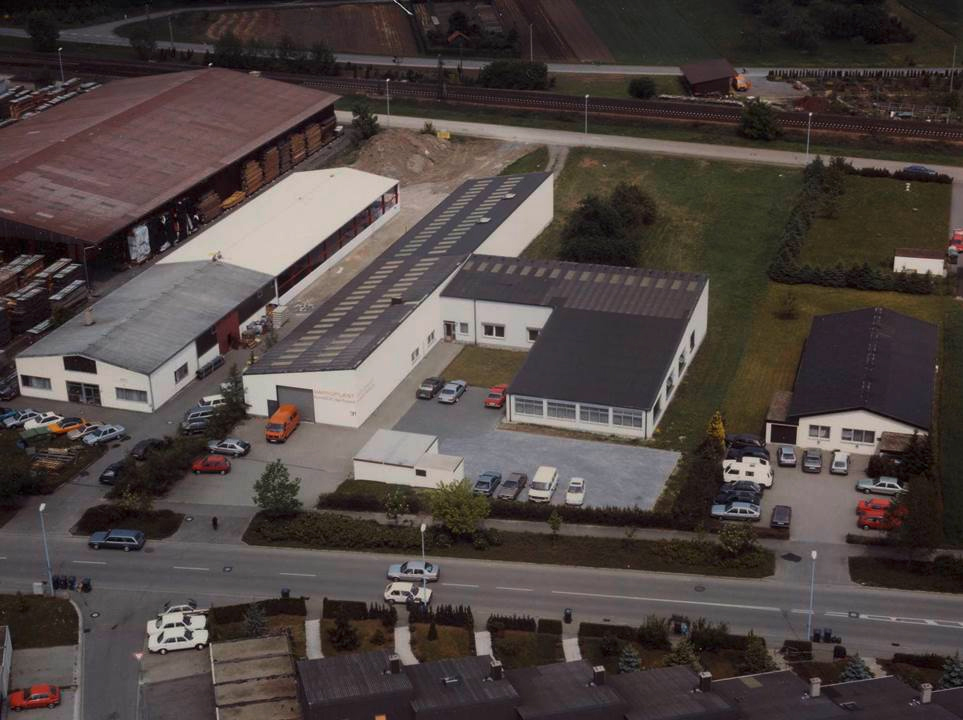
1985
Introduction of hot stamping technology
1988
Konrad Däbritz invents the VARIOLIFT® a lever system for injection moulds within the injection moulding machine
1990
Introduction of pad printing technology and ultrasonic welding
1992
Warehouse extension
1994
Dipl.-Ing. Michael Däbritz is appointed as an additional managing
director.
Introduction of 2-component technology in injection moulding and screen printing technology
1995
On 24 December 1995, the company founder Konrad Däbritz passes away after a serious illness at the age of 58. Shortly before his death, he set the company on course for further growth and built a new production hall to expand the injection moulding technology. His two sons Michael and Roger take over an excellently managed company and continue to run the business successfully to this day.
1997
Auditing according to DIN ISO 9001.
2000
Start of the "painting technology" era, purchase of an automatic spindle painting machine.
2002
Acquisition of two neighbouring properties and buildings to the east.
2003
Connection to the neighbouring building.
Acquisition of an
automatic surface spraying machine.
2004
Introduction of laser labelling technology (day-night design).
2005
Takeover and integration of the company "Bika Thermoformtechnik" into
VARIOPLAST® Konrad Däbritz GmbH.
Geothermal drillings for cooling and heatings
2006
Development of our own mould construction.
Conversion of the building heating system to environmentally friendly heat pump technology utilising the
geothermally stored waste heat from machinery.
Introduction of high-frequency welding
Production of silicone rotary dampers.
2007
Installation of an exhaust air purification system (TRNV) for the paint shop.
2008
Auditing in accordance with DIN ISO 14001 (environmental certificate).
2009
Investments in automation, articulated arm robot technology, robot painting, ESD assembly areas and expansion of the injection moulding machine park into the clamping force range above 4000 kN.
2010
VARIOBOXX® - innovation in the reusable packaging sector: lightweight,
customisable, cost-effective and environmentally friendly.
INSTANTCOAT® - Introduction of an inline process for injection moulding, coating and packaging in record
time and quality.
New injection moulding plant in Ötisheim.

2011
Construction of a new logistics hall,
Extension of the machine clamping force range to 550 tonnes,
Installation of further INSTANTCOAT® coating system
2012
Construction of a new warehouse, expansion of the thermoforming department, introduction of PVD coating of plastic parts with UV coating
2015
New mold construction, administration and storage rooms
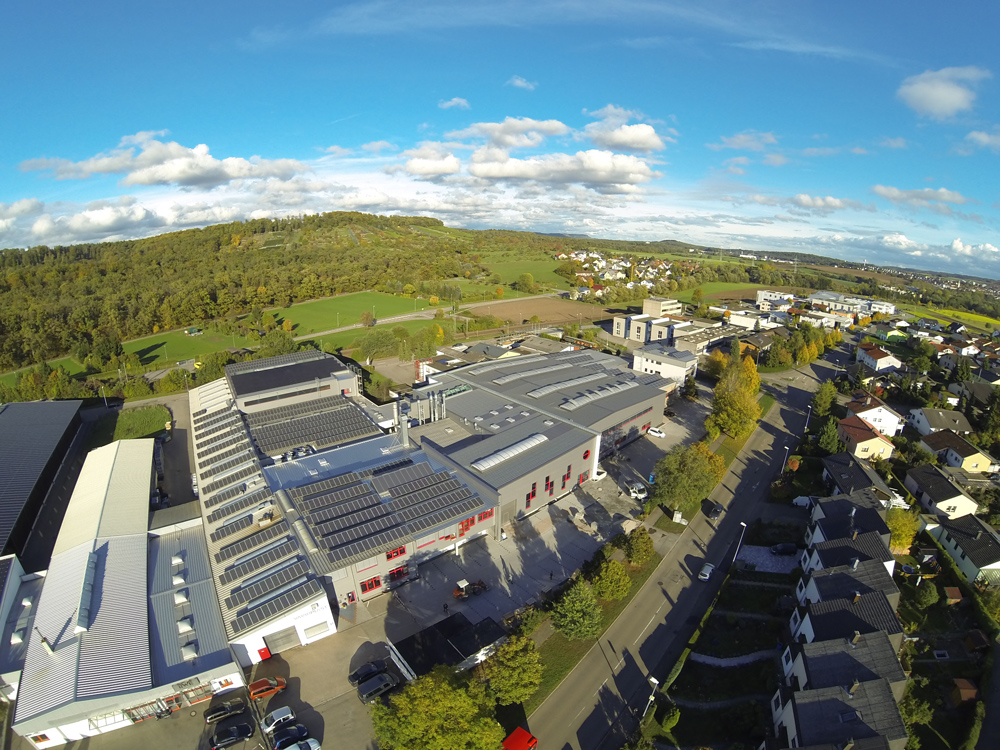
2016
Introduction of robot-guided foaming of seals
Acquisition of another neighbouring property
Acquisition of an 18,000 square metre site in the Ötisheim industrial estate Industriestraße for the
long-term to secure our growth opportunities
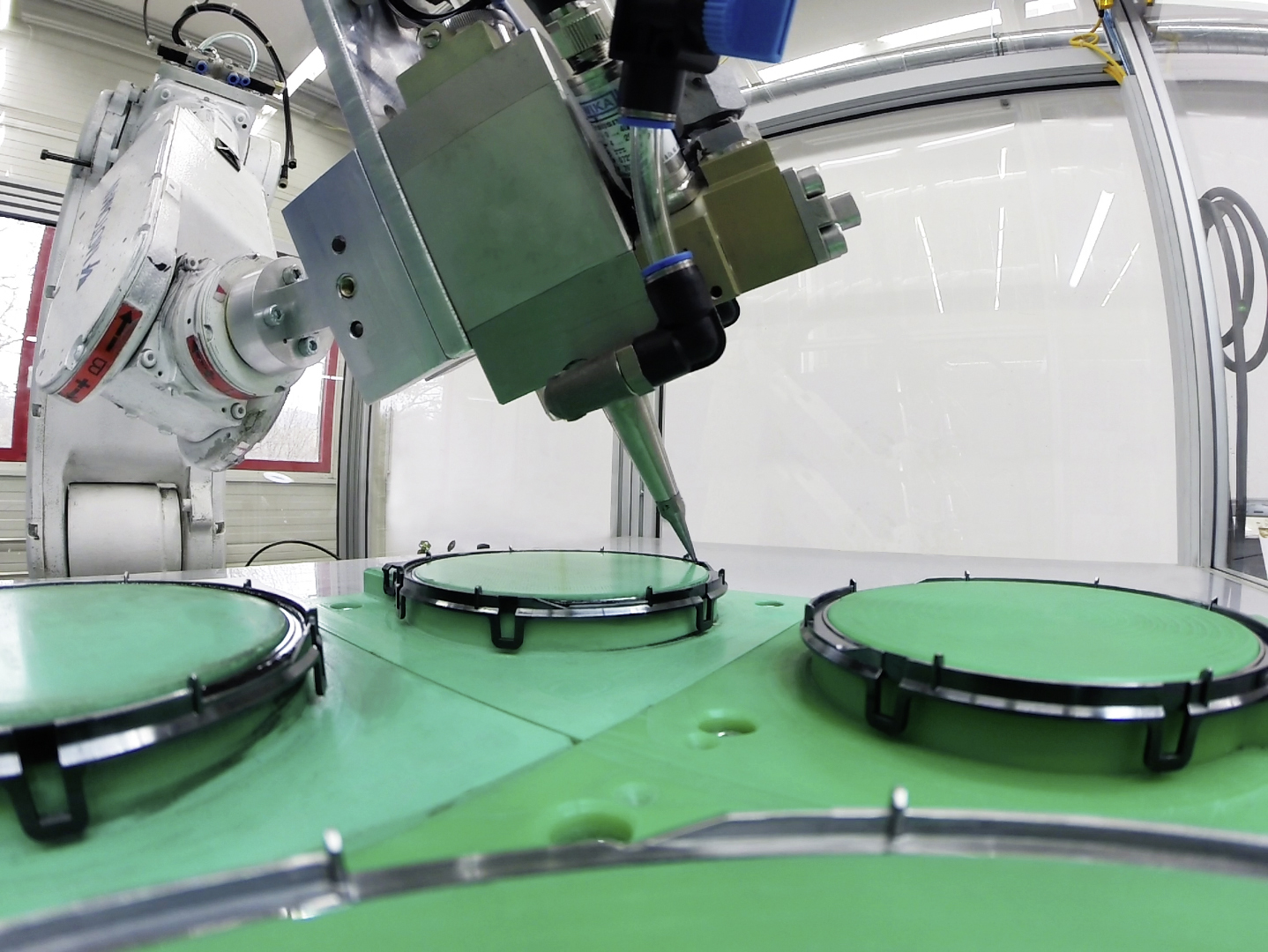
2017
Expansion of the centralised material supply
Commissioning of a further injection moulding hall (air-conditioned)
Commissioning of our fifth instant coating system for injection moulding and coating plastic parts for
head-up displays.
2018
Patented TURBOTHERM® variothermal process
Installation of air conditioning in our production hall
IATF 16949 certification
2019
New PVD system for parts up to 200x300x400mm
Introduction of "Black Panel Technology"
2020
Inline polishing
2021
Fully automatic inline painting for 2 coats of paint with
CO2 pre-cleaning
Conversion of the injection moulding machine park to all-electric
2023
Completion of the new logistics hall
Expansion of the existing PV system to 600 kWp
Managing Director Michael Däbritz takes over all company shares.
His son, Pierre Däbritz, is now a plastics engineer
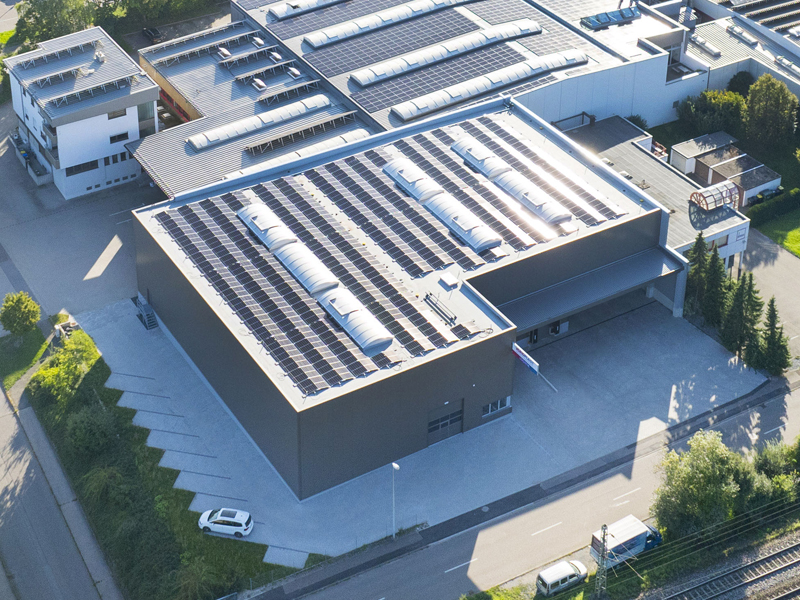
2024
Foundation of the company VARIOPLAST GmbH for customers from the non-automotive sector
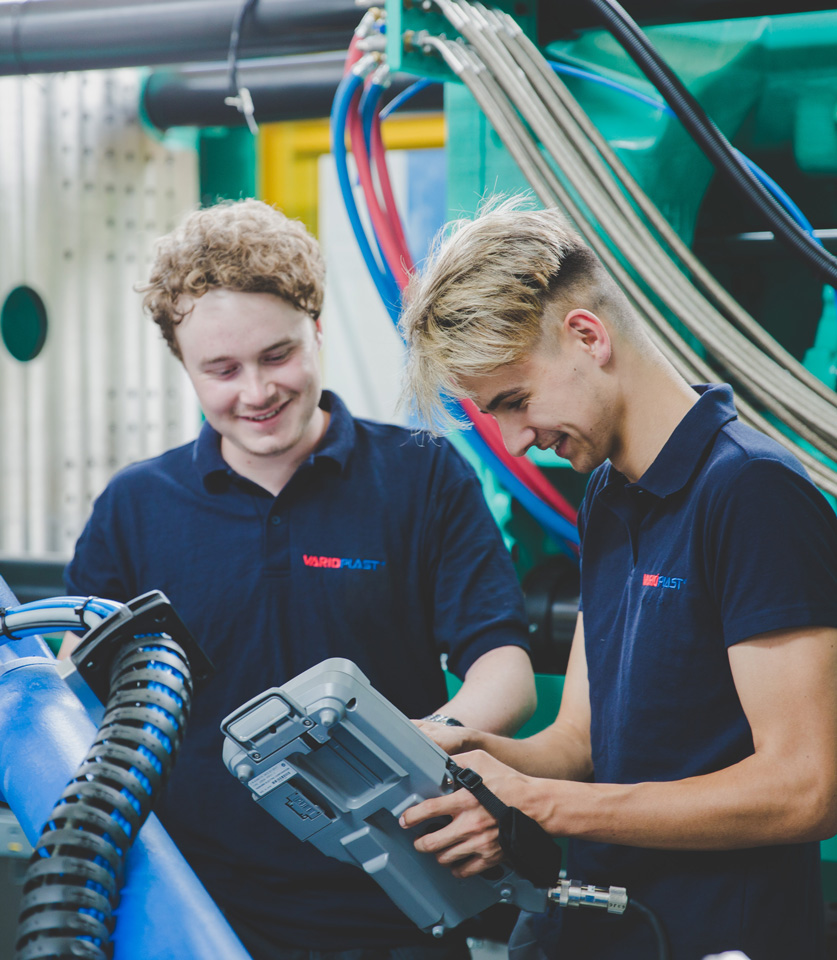
Career
Start your career at a leading innovator of the industry!
As an innovative and growing company in plastics processing we are continually looking for young talent.
Varioplast GmbH
Varioplast Konrad Däbritz GmbH
Varioplast Co. Limited (HK)
Varioplast Holding GmbH