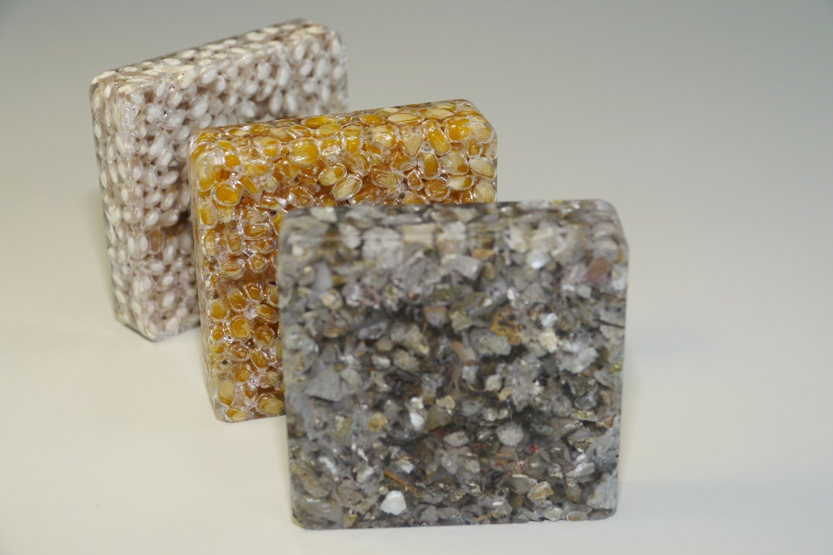
Patents and Procedures
VARIOBLEND®: Hybrid process for the recycling of plastics
The problem:
How can we recycle mixed plastic waste and painted thermoplastic waste? How can we recycle without using expensive, polluting or environmentally hazardous media?
VARIOBLEND® answers these questions and offers the perfect solution.
The process: a combined process for a wide variety of bulk and filling materials and even mixed production waste for thick-walled injection moulded parts.
The bulk material can, for example, consist of mixed thermoplastic waste and even painted plastics. A wide variety of free-flowing and coarse-grained fillers can be used, such as any plastic granulate, glass beads, metal granulate, fine gravel and even coffee beans and corn kernels!
...In this way, any visual and functional effects can be achieved.
In a patented combined process, bulk material is first fed into the cavity via gravitational force and finely dosed. The filling material is then injected. Only approx. 30% of the remaining volume needs to be filled.
Environmentally friendly, cost-effective and thick-walled are no longer a contradiction in terms!
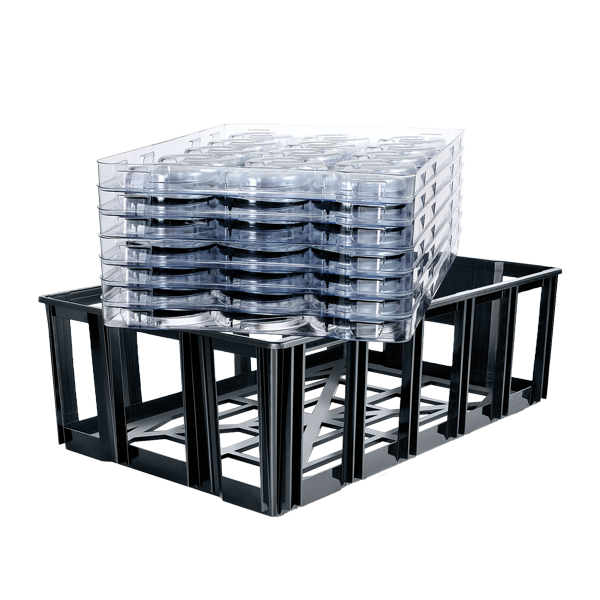
Packaging engineering
Protective packaging VARIOBOXX®
product specific, custom made and eco-friendly packaging
Our patented VARIOBOXX® is a lightweight product specific reusable packaging made from recycled material. It is a combination of standard and customized packaging: Standard is the stacking box (stable injection moulding part, 1/4 or 1/8 of Euro pallets) and the inlay can be cost-effectively customized according to demand (thermoformed part).
In total significantly more cost-effective in respect to purchasing as well as to any specific costs for inlays and transportation in comparison to previous solutions, at the same time significantly more lightweight, transparent, inexpensive, individually customizable as well as eco-friendly.
VARIOBOXX® has been patented since December 2011.
Advantages
- transparency: filling visible and controllable
- lightweight: empty weight approx. 1.5 kg incl. Inlay and Cover
- customized: Frame (carry box) in different colours, inlay and cover individually formed
- robust: shocks and blows are damped and mostly neutralized by the frame
- dust-proof: the cover fits exactly onto the inlay and closes it
- suitable for block storage: the box is dimensioned to 1/4 or 1/8 of a Euro pallet and is optimally stackable
- four sizes: 600 x 400 x 195 mm | 600 x 400 x 265 mm | 400 x 300 x 195 mm | 300 x 200 x 195 mm
- inexpensive: 1 Truck saves approx. 2 l Diesel/100 km
- eco-friendly: ca. 2 kg of CO2 saved/box during production and approx. 5 kg of CO2 /Truckload per 100 km compared to standard packaging
Patents and Procedures
Inline PVD metallisation: decorative, functional and selective nanocoating, Cr6-free and eco-friendly
„The INLINE-metallization process INSTANTCHROME® by means of PVD, developed by VARIOPLAST®, is a perfect fit for our strategy of INHOUSE-process chains and has replaced galvanic chrome plating in our company.“
Dipl.-Ing. Michael Däbritz
Manager of VARIOPLAST®
Production cells have been developed for this inline metallisation process that integrate all process steps from injection moulding to painting, lasering, printing, PVD metallisation and packaging of the product.
Like all our inline process chains, these can also be extended with any processes that are sometimes not possible with galvanic chrome plating:
- Ultrasonic welding and/or other joining techniques
- Day/night design lasering
- Base coat (primer)/drying
- Top coat (decorative protective varnish), UV varnish...
The reproducibility and consistency of the process conditions offer maximum quality benefits as well as time and cost savings.
Patents and Procedures
Inline coating: decorative single or multi-layer coating
"By direct and fully automated linking of injection moulding, coating and final packaging with INSTANTCOAT® Plus we have reached the presently conceivable optimum in efficiency and product quality."
Dipl.-Ing. Michael Däbritz
Manager of VARIOPLAST®
Production cells have been developed for this inline coating process that integrate all process steps from injection moulding to coating, lasering, printing and packaging of the product.
Research & Development
Cooperation with Colleges/Universities
Variothermie with the new TURBOTHERM® process.
University of Karlsruhe – Bachelor thesis at Varioplast
Further cooperations with the universities of Ulm and Darmstadt
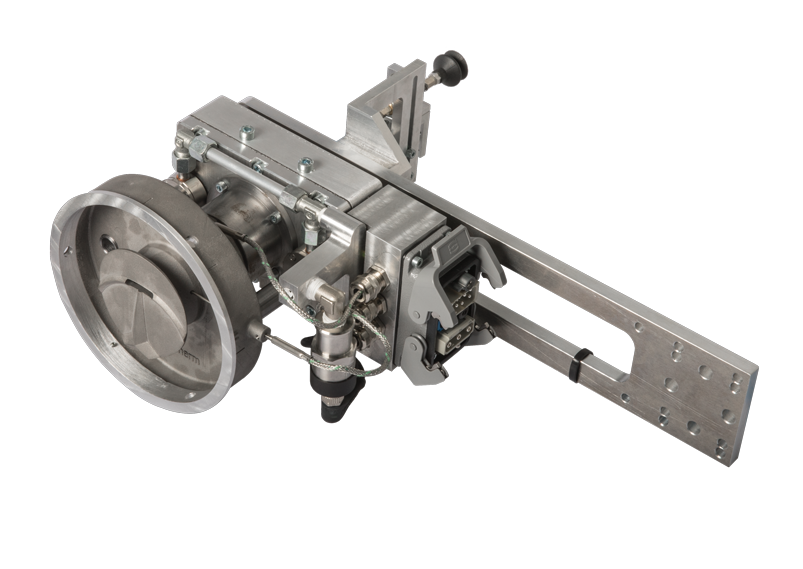
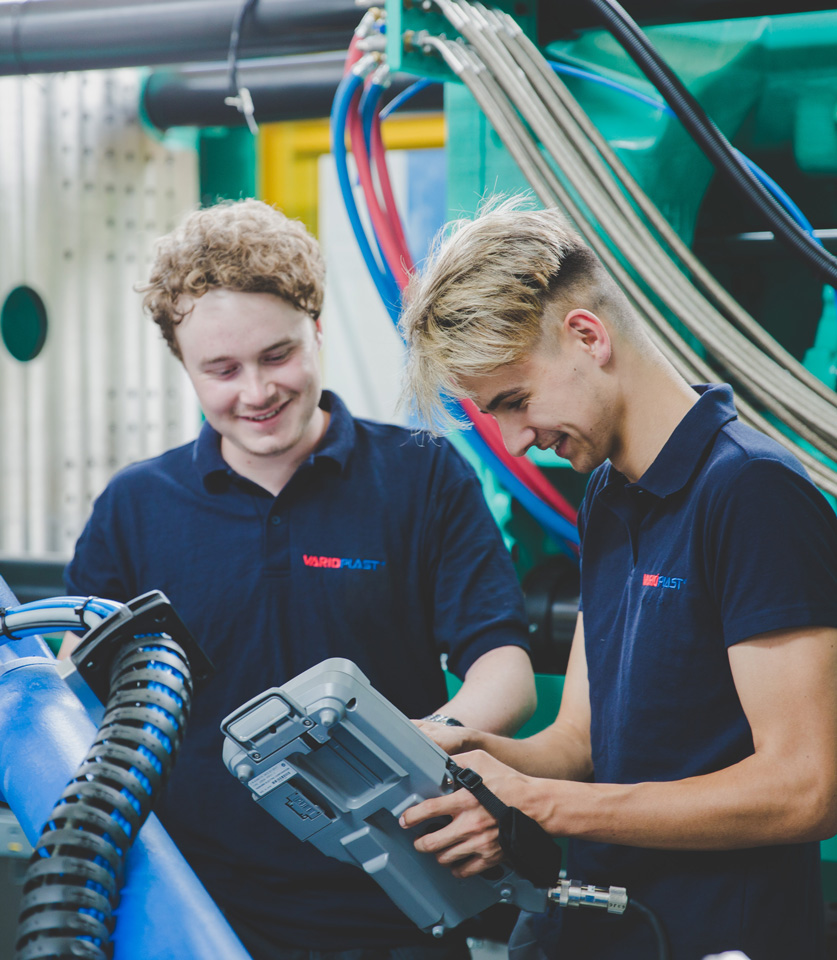
Career
Start your career at a leading innovator of the industry!
As an innovative and growing company in plastics processing we are continually looking for young talent.
Varioplast GmbH
Varioplast Konrad Däbritz GmbH
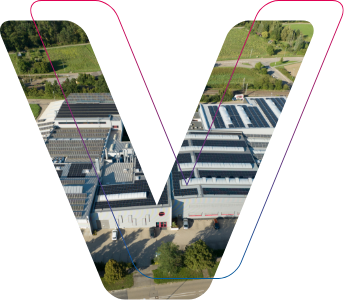
Follow us
Varioplast Co. Limited (HK)
Varioplast Holding GmbH